Bombardier Aviation's aircraft manufacturing factory is a typical successful application of 'Labor Bubbles' to maintain operations while keeping safe for employees.
Bombardier Aviation, aircraft manufacturing company with 22,000 employees of 7 factories in Canada and the US, in April, was voted by the Quebec Chamber of Commerce (FCCQ) as one of the winners of the tournament
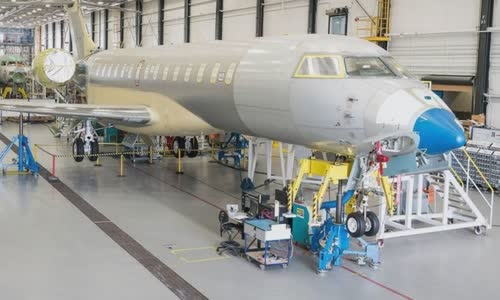
Photo: Bombardier.com.
Bombardier was awarded for creativity in efforts to ensure safety for workers and employees at its factory in front of Covid-19 pandemic.
Bombardier's workout model has been studied by researchers at Calgary University in an analysis published in the Journal of Canadian Medical Association.
Inside a plane factory of Bombardier Aviation.
The moment Covid-19 excavates in Canada last year, the company has a factory located in two most affected cities in Montreal and Toronto.
The factory must close three days to carry out the whole disinfection and traces the workers with contact with infections.
Because aircraft manufacturing is a long-term business operation and it is necessary to invest significantly to transport inventory, so the reduction of production cycle time is very important.
Hundreds of employees join a building for a narrow period.
The process of compulsory workers must be close contact, especially when they fabricate aircraft furniture or installation of important parts.
According to experts from Calgary University, the bubble model, with the key is the labor force divide into working groups based on preventive and functional principles, which can both ensure safety for employees
In Bombardier, office blocks such as engineers, financiers, managers, programming, forced to work remotely.
With the above workers, Bombardier stool They work in a combination of a number of rules, forming separate bubbles.
The functional bubbles have the number of employees required to complete the lowest job.
Bombardier also ensures isolated factors by arranging employees' outgoing hours so that no two groups appear at the same time, and limit access to common areas such as changing rooms or houses
Similarly, Bombardier also sets out that every worker group is not allowed to move freely between different subdivisions that must be in a certain area to minimize further interaction.
In particular, Bombardier increases working time in the week of each group from CA 8 hours to 10 hours.
To protect employees further and reduce the ability to spread, the bubble mechanism in bubbles is also set.
Although this is a safe key, it also raises challenges to organizations organized by employees with different skills and expertise often needed in different parts and groups.
Besides the worker bubble model, the daily symptom examination for workers is also a good way to reduce the probability of outbreaks at work.
In Malaysia, the government in March also issued a safe labor bubble initiative.
Labor exposure close to positive cases will be taken to a separate house separate from the community and other workers until they have a negative result again.
The company management is responsible for creating bubbles at workplaces and workers' accommodation, and ensuring that the movement of close contact workers is safe and does not cause any pepper impact
Some other points of the initiative include establishing emergency reaction teams made by the company to prepare and accurately apply the processing process, as well as regular inspection and supervision.
The company also needs to conduct a continuous plant disinfection, mobilizing means available to transfer workers and workers.
If the workers are carefully managed, a Covid-19 positive employee can inform employers and other colleagues in his bubble to be isolation.